Oil sands development conjures images of giant trucks and shovels toiling in massive, open-pit mines. The fact is, over half of the production from Alberta’s oil sands occurs through in situ development, where wells are drilled to extract an extra-heavy type of oil—what those in the industry recognize as “bitumen.”
While some bitumen can be pumped to the surface using conventional techniques, most is too “viscous,” or dense, to produce (or move) without the help of steam. As is the case with any type of energy resource development in Alberta, it’s up to the AER to ensure that all such operations follow the rules and stay up to date on regulatory standards.
Here are five things to know about in situ development:
- Latin roots. In situ methods separate the oil from the sand underground, or “in place”, which is what “in situ” means in Latin. Most in situ oil sands recovery uses steam and is referred to as thermal.
- A deeper dive. About 80 per cent of Alberta’s bitumen reserves are buried too deep to mine and can only be recovered through in situ methods by drilling wells. Because the process of recovering the bitumen occurs underground, in situ’s surface impact is far less than that of mining operations.
- Technologically speaking. Most in situ oil sands operations use a lot of water to create steam. The two main technologies operators use to produce in situ oil are steam-assisted gravity drainage (SAGD) and cyclic steam stimulation (CSS).
- In a SAGD project, two horizontal wells are drilled about five metres apart, one over top of the other. Steam is injected into the top well, which heats the oil until it’s mobile enough to be produced from the lower well.
- CSS involves injecting steam into a vertical or horizontal well with enough pressure to fracture the rock, which allows the steam to move rapidly into the reservoir. This heats the bitumen and reduces its viscosity, allowing it to flow more easily. The bitumen may then be produced to surface using the same well.
- Recycle, reduce, reuse. After the steam has done its job, it must be separated from the oil. The mixture is transported by pipe from the well to a plant, where this separation takes place. The steam is then recycled for its next use—in other words, it is converted back to water and treated. The AER makes sure that water is used efficiently by requiring most operators to recycle and reuse as much water as they can. On average, operators recycle 90 per cent of the water they use.
- Keeping a lid on it. The idea is that the oil, along with the steam that’s been injected underground, must not escape. Caprock—made up of a low permeability, fine-grained rock such as shale—is what keeps the steam and oil contained underground. This is critical to ensuring safe operations, protecting the environment, and ensuring that the oil is not wasted.
The AER requires that in situ operations recycle as much water as possible; on average, companies recycle 90 per cent of the water they use.
Steam-assisted gravity drainage (SAGD)
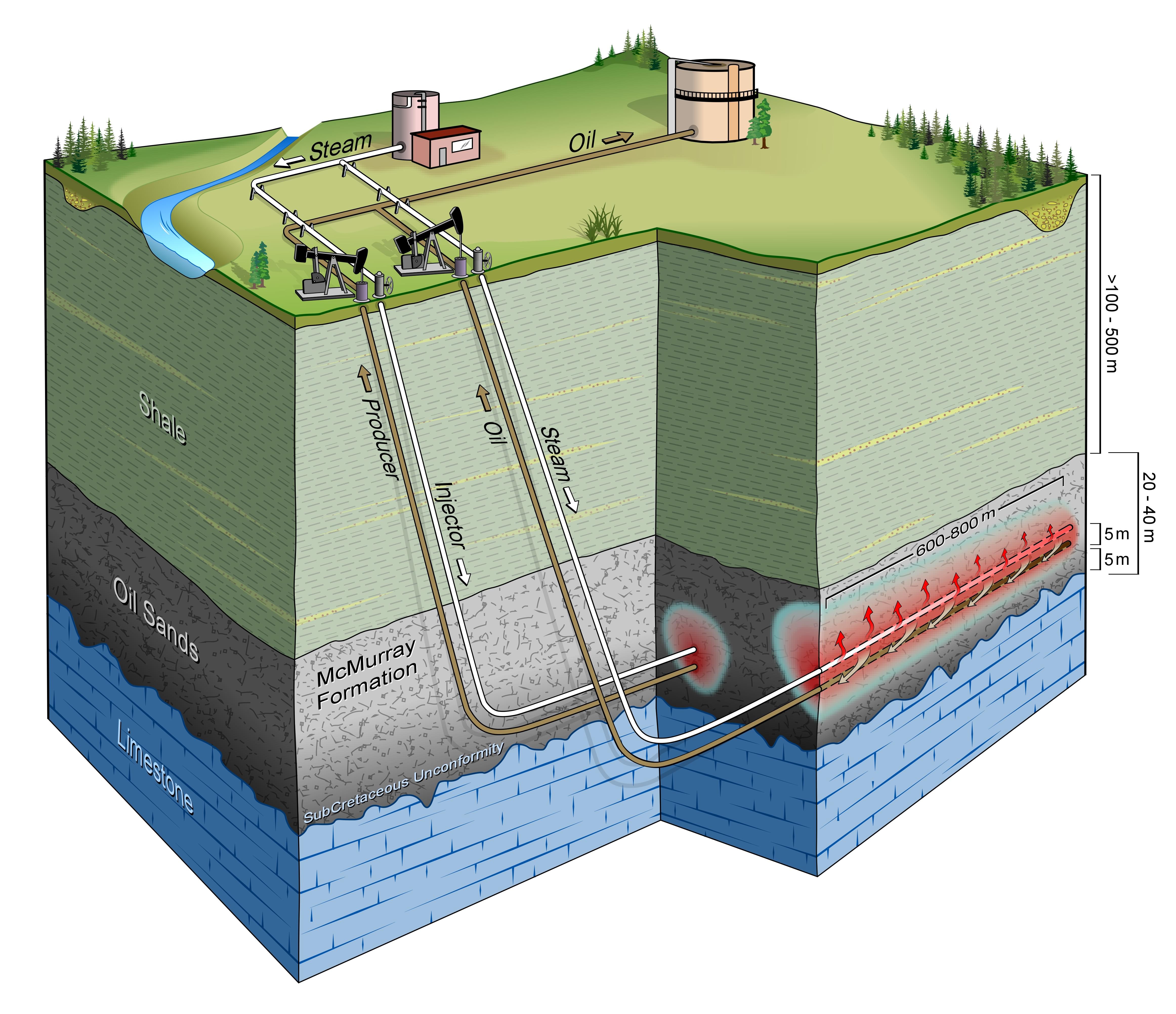